Uplifting blog
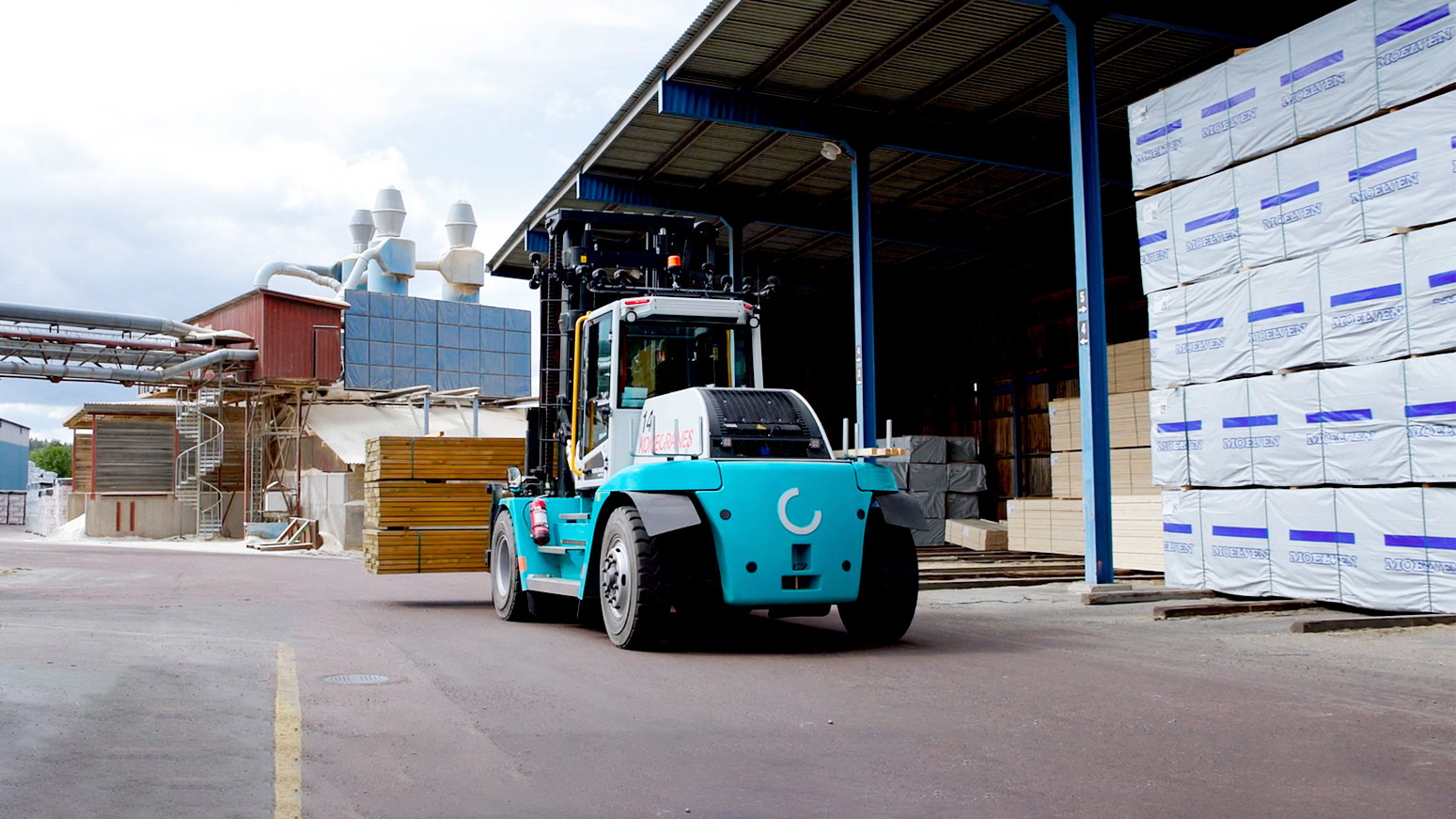
E-VER Developing an emission-free answer to modern industry challenges
Electric forklifts are nothing new. But capable of lifting 10-18 tons? Until recently, lifting in this weight class and higher was only practical with diesel engine powered machines. The lead acid batteries used in smaller forklifts are not power-efficient enough to take on the job — the battery size and weight required for heavy industrial applications would negate any energy gains. Lead acid batteries also require longer time for charging.
These days, with an increasing pressure to lower CO2 emissions, more companies want an alternative to diesel. Now they have it—with the Konecranes E-VER electric forklift, powered by lithium-ion batteries to make emission-free industrial lifting possible.
Getting serious with Li-ion batteries
With the rapid advances in lithium-ion battery performance of recent years, technology had caught up to ambition for the R&D teams at Konecranes. “On these bigger machines, you need much larger batteries, ”says Anders Nilsson, Director of R&D and Technology. “One of our main concerns was getting good endurance from a battery charge. Lithium-ion are more efficient because they have lower power losses and can be fast charged.”
From a development perspective, the specialized battery requirements, including reuse and recycling considerations, meant the right choice of partnerships was critical. “The supplier we chose could demonstrate superior sustainability performance,” says Anders. And while sustainability was important, it wasn’t pursued at the expense of innovation or reputation. “We introduced a lot of new solutions never before seen on the market, such as new traction and thermal management systems. And always at the back of our minds was that we’re known for high-performing machines—It was important that E-VER still deliver the performance our customers expect from a Konecranes.”
Anders Nilsson, Director of R&D and Technology and
Lisa Martinsson, Senior Project Manager and Program Manager for Electrification
Making it work together
Impressively, E-VER development partly took place through a global pandemic. That raised a lot of concerns early in the process. “Our teams are all over the globe, and the project was complex,” says Lisa Martinsson, Senior Project Manager and Program Manager for Electrification. “But being forced to work digitally brought us together in a way no one could anticipate.”
They also learned that sending prototypes to the remote R&D office was another strong way to unite the teams. “We sent the unit to Italy for commissioning, something we hadn’t tried before but will continue to do,” says Lisa. “When E-VER was ready, we gathered online together to watch the first turn of the wheels. It was a big thing.”
Lifting for the electric future
E-VER is a game-changer for industrial-capacity lifting that will only grow into more. “We’ve just started on the electrification journey,” says Anders. “We have bigger machines and container handlers, and they’ll all be electric at some point. There’s a big shift in technology in our industry.”
Something Lisa looks forward to as well. “We are on a fantastic journey with a fantastic team,” she adds. “It’s really fun coming to work every day knowing you’ll learn something new.”
Watch the full E-VER development interview with Lisa and Anders >>
Learn more about the evolving power of electrification >>
Related Articles
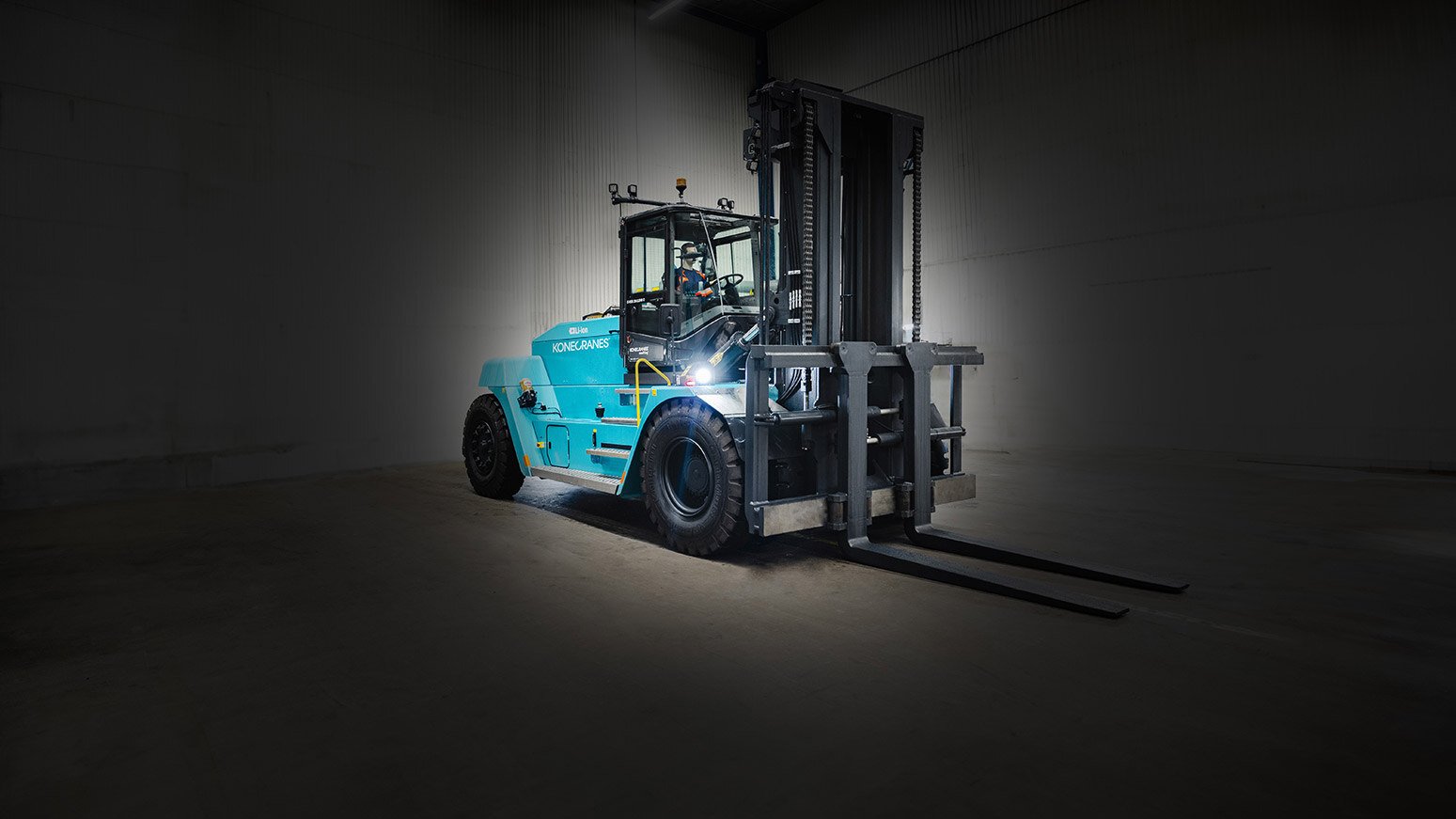
Introducing our most powerful electric forklift E-VER. Again!
The global trends are clear: to combat climate change, everyone must actively contribute to...
2 Minute Read
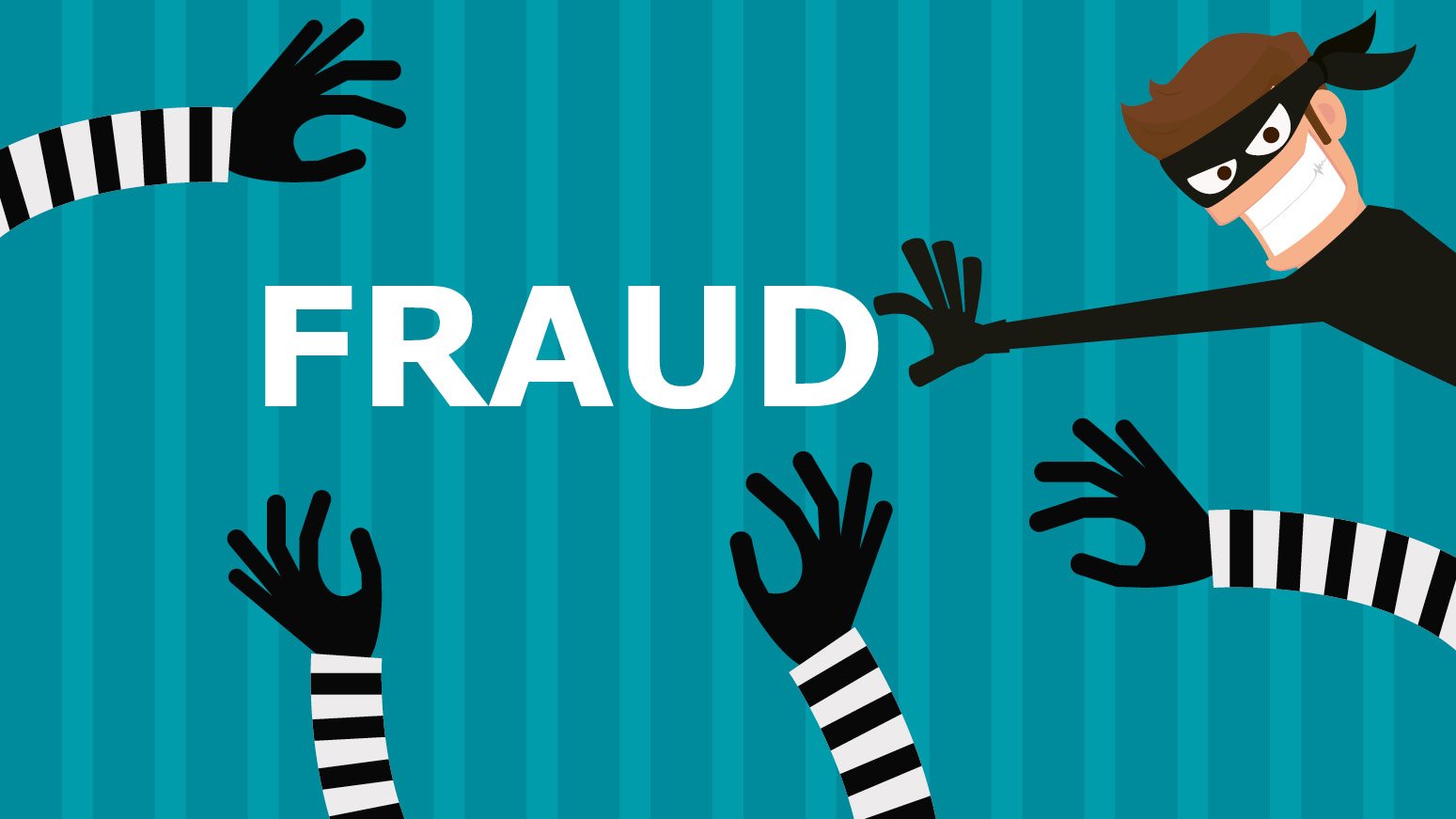
Protect your equipment, business and customers from spare parts fraud
According to a study by the OECD and the EU Intellectual Property Office (EUIPO), trade in...
2 Minute Read
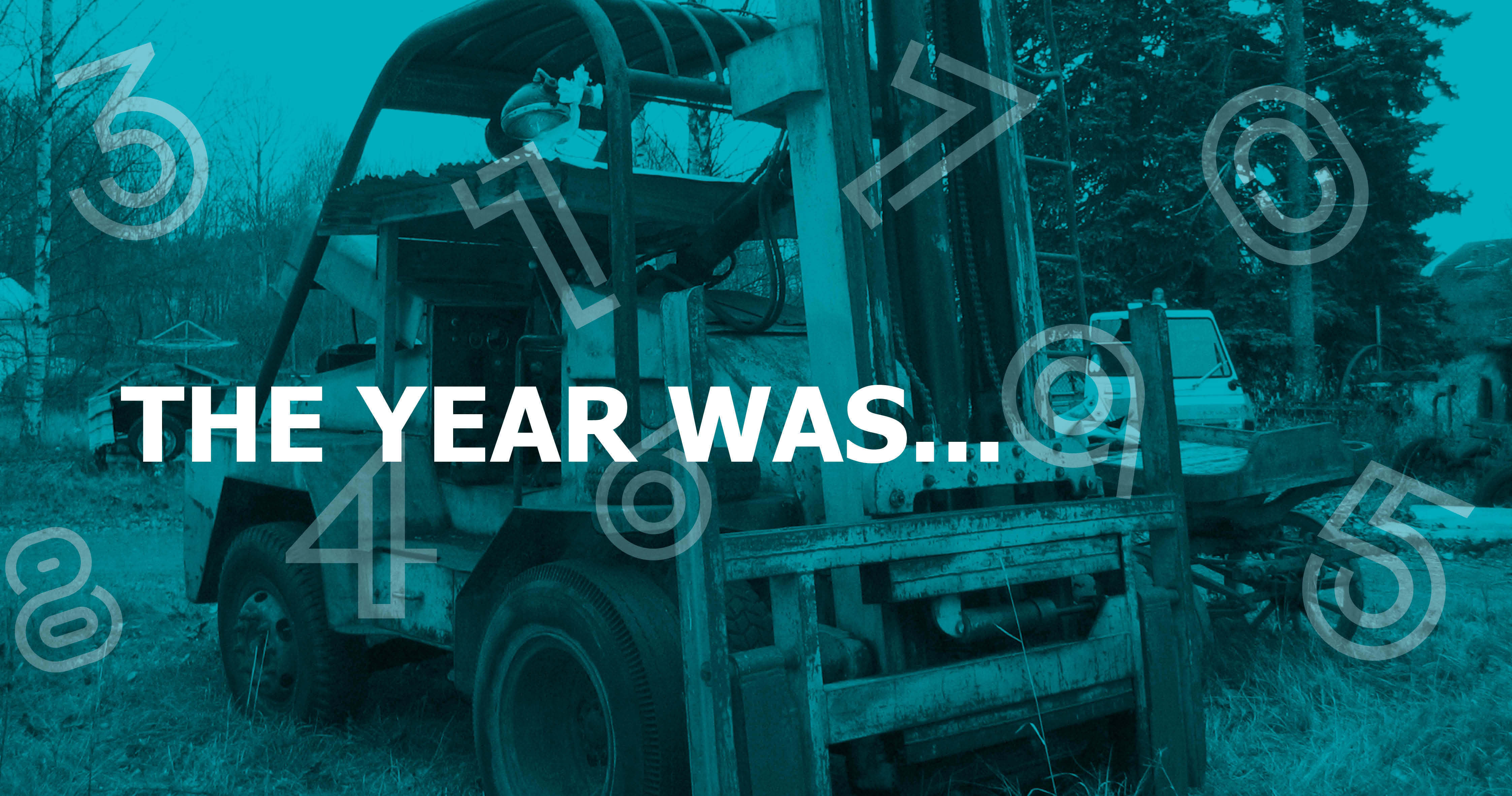
1956 – A new era of containerization
The shipping industry has been around for centuries, and during all those years goods were...
2 Minute Read