Uplifting blog
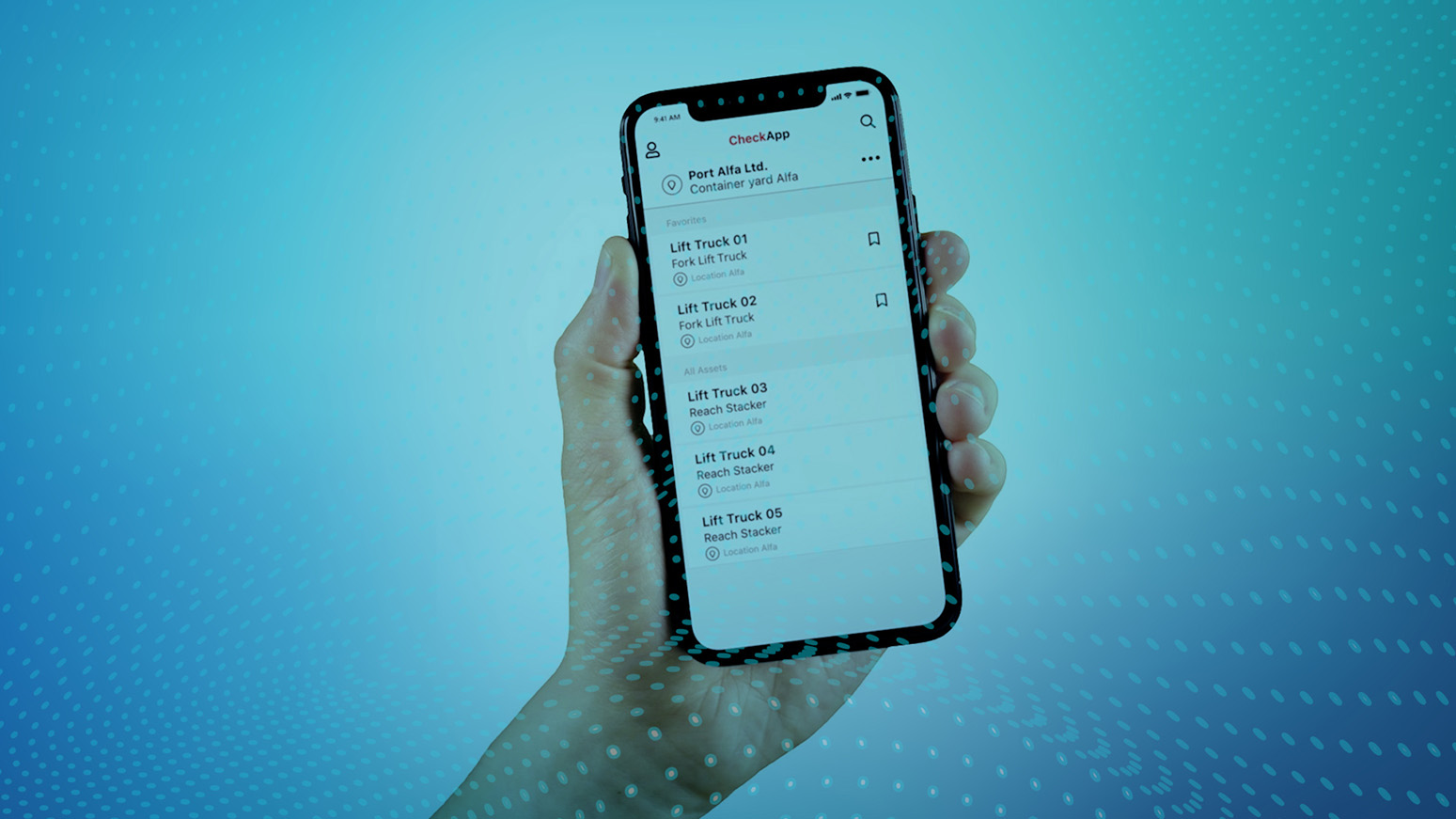
It's time for inspections to go digital
For as long as we’ve had heavy machinery, we’ve had daily and periodic inspections to make sure they’re in working order and safe to operate. In many markets, it is a legal requirement. And with good reason—inspections are critical to safety, maintenance efficiency, pre-emptive troubleshooting, managing costs and optimizing the lifetime of the machine.
CheckApp is a powerful tool for performing them quickly and accurately using a smartphone or tablet. Even if your fleet is mixed, the results from your digitalized inspections will be saved to and benefit from the sharing and alert capabilities available through the yourKONECRANES.com account the data is uploaded to.
Phone power
Imagine you could simply pull out your phone or tablet, follow a few pre-set prompts and instructions, include audio messages, photos or videos, and upload the daily inspection form to be shared instantly with managers and maintenance.
“It’s definitely time for inspections to be digitalized,” says David Andersen, Global Training and Documentation Manager. “It solves the headaches of finding and delivering paper inspection forms, knowing what to do and how, and communicating issues to the right people quickly. No one can afford to lose that kind of time these days.”
David is part of the Konecranes team that developed CheckApp. “CheckApp makes life simpler for operators, managers and maintenance teams. It’s just so easy to download the app, and it can be used with any machine—Konecranes or not.”
A few minutes
Digital tools like CheckApp streamline a process everyone should be doing anyway to protect staff and equipment, and potentially avoid costly downtime for service or repairs.
“The big advantage is it makes inspections faster,” says David. CheckApp follows a pre-set and customizable check list that is uploaded as soon as it’s done to yourKonecranes.com. “Operations and maintenance managers and/or anyone who needs to know, gets the info at the same time and decides whether to take immediate action for urgent issues or wait until the end of the shift or when the regular/scheduled service is due.”
It’s a few minutes that gets the day or shift started off right.
The app also provides instructions and prompts the operator to check in a pre-determined order, purposely designed to minimize unnecessary back and forth. Depending on your machine, it could take a few minutes for a comprehensive walk-around—with the results available instantly to the entire team.
And because the machine’s inspection and service history is recorded in every detail, the residual value of the equipment might also increase.
Easier to do than not
Because digital tools like CheckApp speed up and simplify inspections, they also incentivize operators and service personnel to follow procedures properly.
“If an engine fails unpredictably, the questions will come,” says David. “Why didn’t we see that coming if we have inspections?”
The app confirms every step of the inspection is done, because it prompts the operator to do so and doesn’t upload the report until the procedure is complete. And the awareness that digitalized procedures are reviewable is often incentive enough to ensure their completion.
Tools like CheckApp also make a lot of sense for markets where inspections are not formalized. Speeding and simplifying the procedure makes the benefit of doing it outweigh the perceived savings of not doing it. That means inspections could be more widely practiced in every market—and that’s better for everyone.
A digital no-brainer
The daily inspection began and has evolved to keep people and equipment safe. To catch small problems before they get a chance to become big ones. And to get the maximum uptime and performance possible from your machines.
Most organizations do it. But very few do it digitally. Considering the low cost of downloading a free app, and the high reward of instant information sharing between teams, that’s bound to change quickly in the coming years. And from a sustainability perspective, the cumulative time, energy and safety benefits could have a positive impact for people, society and the planet.
“It’s the simplest thing we can all do to instantly save significant time, money and resources starting right now,” says David. “Why wouldn’t we do this?”
If you’re a Konecranes customer, you can learn how to use CheckApp at the Konecranes Lift Truck Academy (KLA).
Related Articles
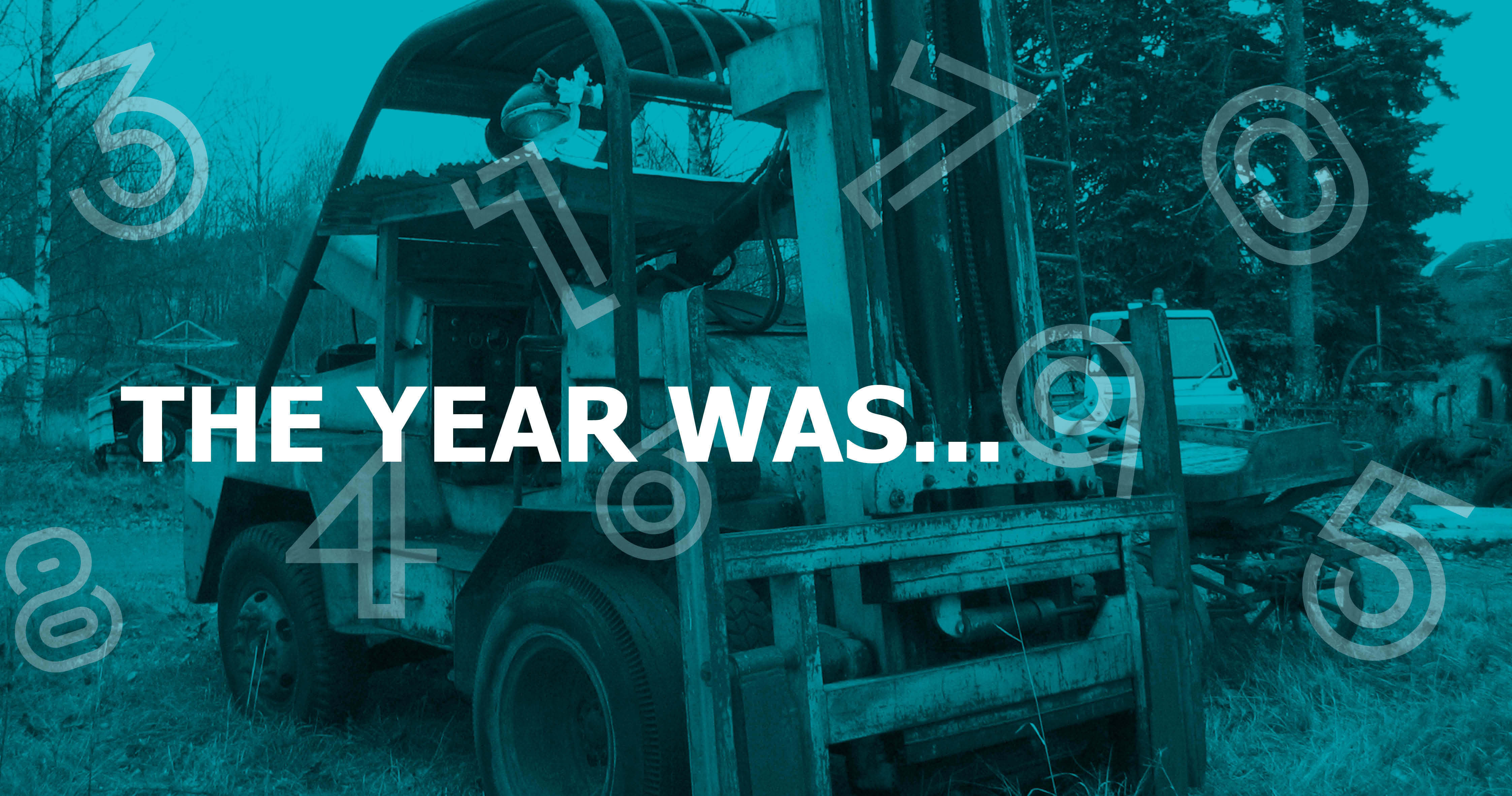
1956 – A new era of containerization
The shipping industry has been around for centuries, and during all those years goods were...
2 Minute Read
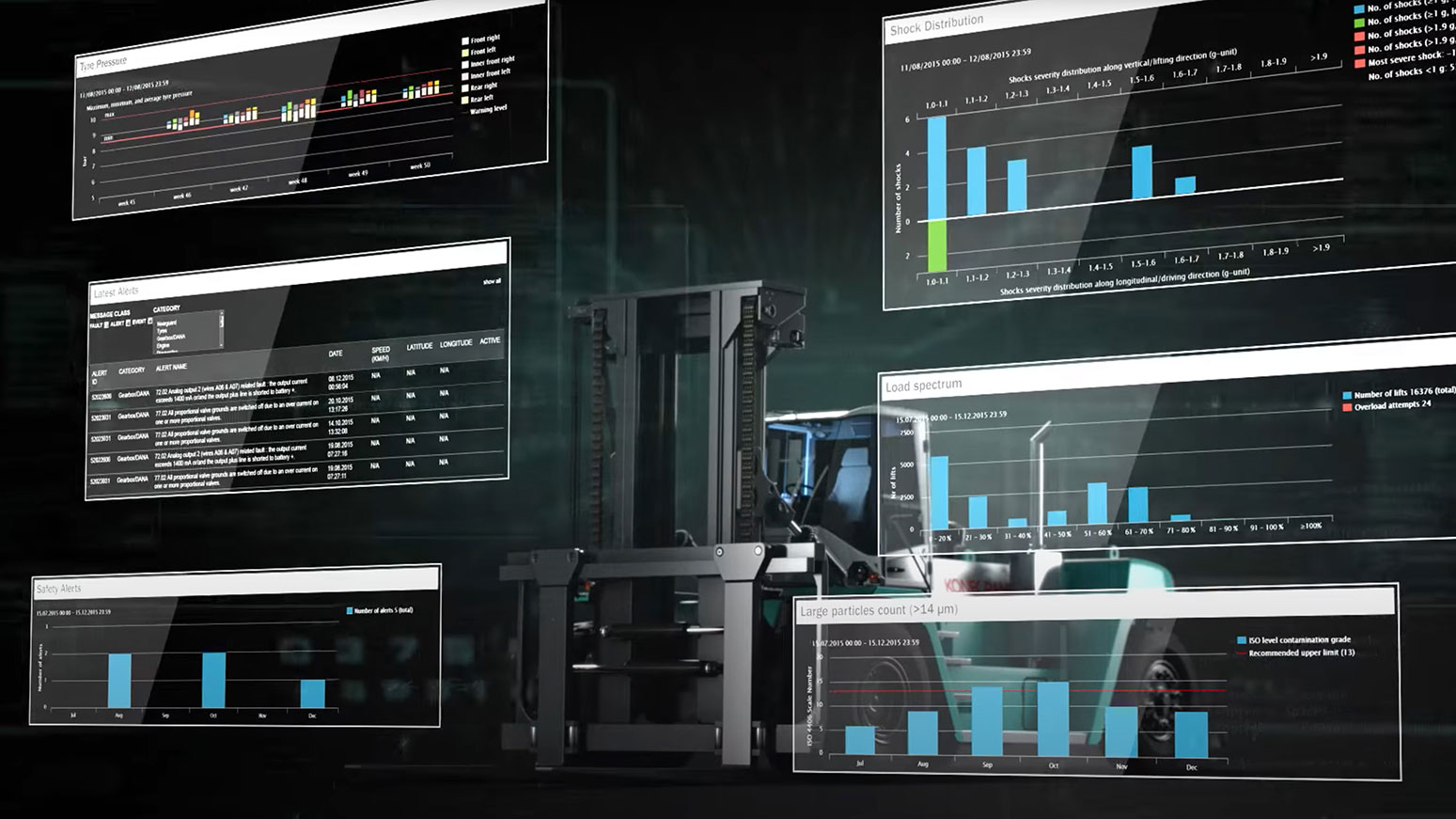
Modernizing industry workplace safety
Generally speaking, workplace safety has come a long way over the years. Largely by learning the...
2 Minute Read
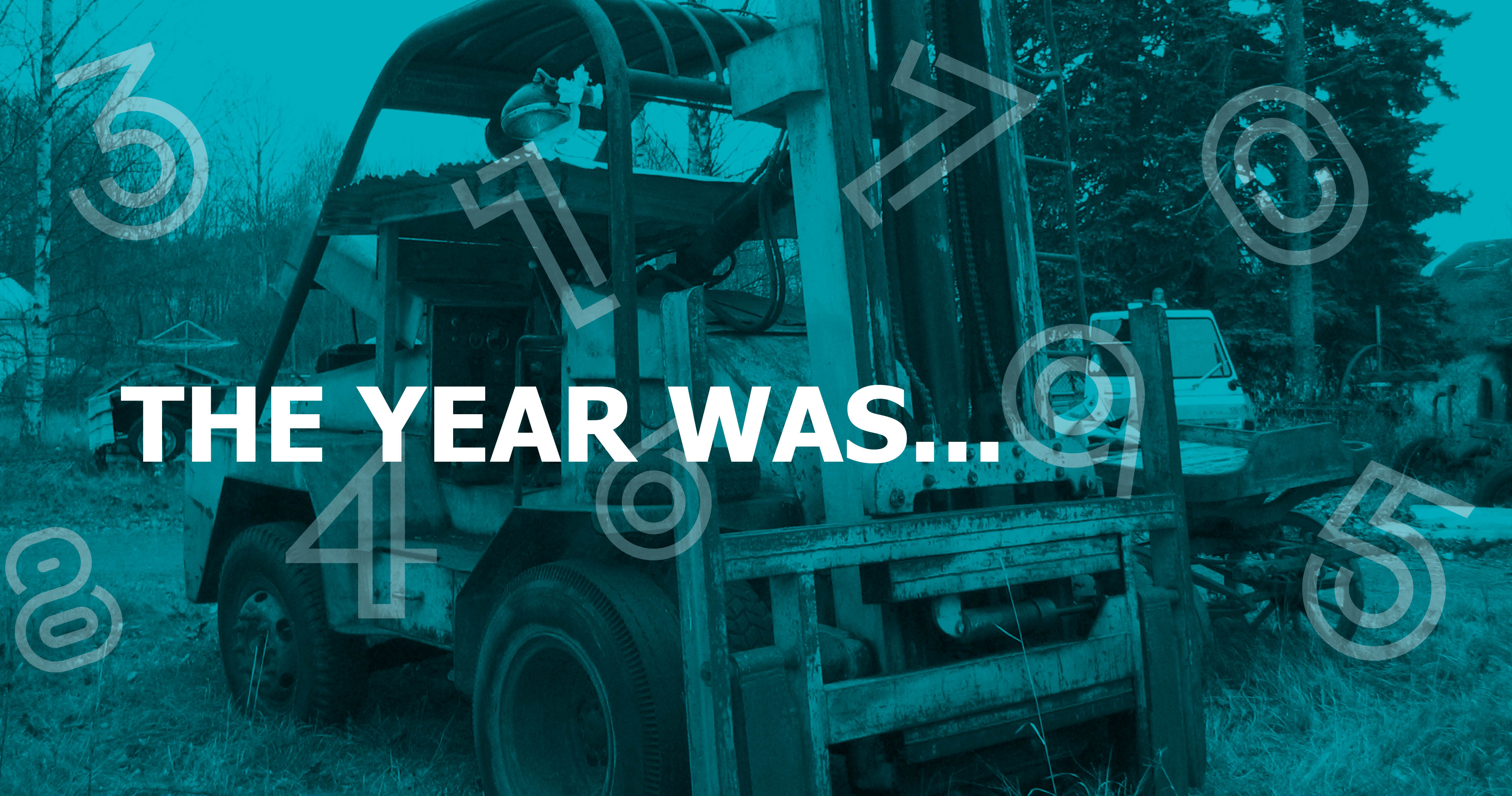
1917 – the very first lift truck is born
Today we see it as a matter of course to use lift trucks and reach stackers to handle goods in...
2 Minute Read